Meet The Maker - Harrison Spinks
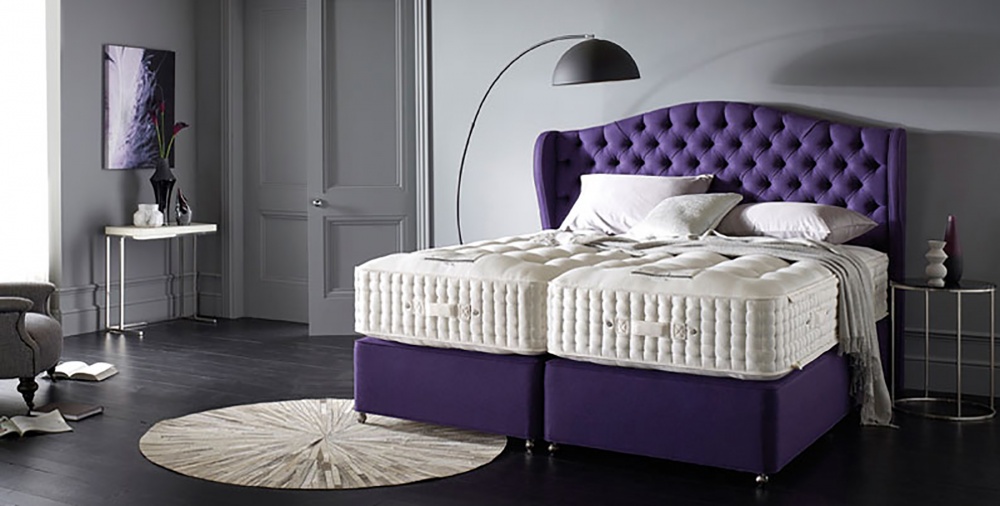
You might not have given your bed or mattress much thought – but you probably didn’t associate beds with farming, cutting-edge technology and generations of history
Tell us a bit about what you do?
As a fifth generation family business, Harrison Spinks is one of Great Britain’s most established and innovative bed makers. Founded in 1840, we manufacture luxury beds under the Harrison, Somnus and Spink & Edgar brands using pioneering technology to develop unrivalled spring counts. Our patented spring technology, combined with sumptuous layers of carefully selected natural fillings, perfectly contour to the shape of a sleeper’s body, to ensure the best night’s sleep possible. I have been at Harrison Spinks since I was 11, and really have grown up with the company. Before working my way up to my current position of Managing Director, I started on the factory floor, just as my father and current Chairman, Peter, did and something my son, Daniel, is currently doing.
Where do you source your materials?
Many of the materials are sourced from our own farm, which is located just 18 miles away from our Leeds-based factory. We don’t source our own materials because it’s easier – it takes a year to grow the ingredients for just one mattress! We do this because the materials’ properties make a better bed, and in turn, offer a better sleeping experience. Hemp, which is grown in our fields, is absorbent and naturally resistant to mildew, while wool, which is reared from our flock of sheep, regulates body temperature, ensuring sleepers are warm and snug in the winter and cool and comfortable throughout the summer.
Can you tell us about the process?
The process starts on our 300-acre Yorkshire farm, where we grow some of our own fillings to be put in the beds. As well as rearing our own flock of sheep from the farm, our large hemp and flax fields are complemented by a unique processing plant. Again, utilising our experience in creating bespoke machinery, we have manufactured our own hemp-processing factory on the farm, which has been tailor-made to match our own specification. The natural materials are baled then transferred to our Leeds factory, where they are carded, before being lovingly handcrafted into beds by our team of experts. Our craftspeople use time-honoured techniques which have been passed down from generation to generation, such as using a 12-inch needle and a lot of patience to perfectly stitch the sides of the beds. It is these kind of accustomed techniques that result in beds that are of the highest quality and represent the best in British manufacturing.
What’s special about what you do?
Our innovative and sustainable beliefs differentiate us from the competition. From owning our own farm, which no other bed manufacturer in the world can claim, to developing the machinery that makes our patented, world-leading springs. The latter has helped us to continue to develop our spring technology – something which has been at the heart of the company since our Somnus brand was the first bed manufacturer to use springs in 1900. This gives us the opportunity to reinvent the way that the springs are designed. As well as patenting our own Revolution and Sensa Intelligent pocket spring systems, our wire drawing machines are continuing to create finer wire, while still offering great durability. Not only does this decrease the weight of mattresses, but allows us to increase our already industry-leading spring counts. Drawing finer wire has led to the development of smaller spring systems, and even if the concept doesn’t work initially, it often leads to new ideas and different thinking. As a company, we’re continuously innovating and that’s what makes us unique.
What’s the best part of your work?
As an inventor, I take great pleasure in working with the development team to dream up new components and ideas to improve the sleeping experience. However, this doesn’t just stop at new beds. Our pocket spring technology has been used in a number of different products, ranging from trainers, to cot mattresses and even sofas. I feel really passionate about our own natural mattress fillings. This led to the purchase of our own 300-acre Yorkshire farm in 2009 – a move which not only enhanced the way people sleep, but made us the world’s first bed manufacturer to grow fillings on its own farm.
What’s the hardest part?
Because we’re a business working within many different divisions, it can be difficult jumping from one moment to the next, trying to get my head around challenges across our diverse organisation. I may have to go straight from understanding an engineering problem in the factory, to looking at plans for the new wedding barn at the farm.
Is there such a thing as a typical day for you?
There’s never such thing as a typical day. One day, I could be at the farm meeting customers and showcasing how we grow our own natural materials, and another I may be working with the development team to invent new spring systems or making improvements to our main production manufacturing processes.
What are you most proud of about your work?
I’m extremely proud of the people in the business who strive to make Harrison Spinks such a vertically integrated company. Even though we have more than 500 members of staff who are dealing with many different areas and projects, we are all one big team, and again, this makes me proud. It really is a mad company, but it works well because we’re a tight knit group, who all work together to ensure the company runs as smoothly as possible.
What are you working on at the moment?
As pioneers in the sector, we’re always working on new innovative products, most of which have been unseen in the industry. We’re currently working on a new mattress suitable for the circular economy. This means we’re not just designing how the mattresses are put together, but how they will come apart. We’re also working on how raw materials in used mattresses can be recycled as a component for a new one, or can even be used for something else. We’re always looking for new and exciting challenges and ways that we can evolve the sector, all resulting in enhanced sleep experiences to ensure the best night’s sleep possible.
www.harrisonspinks.co.uk