Meet the Maker: Skelton Saws
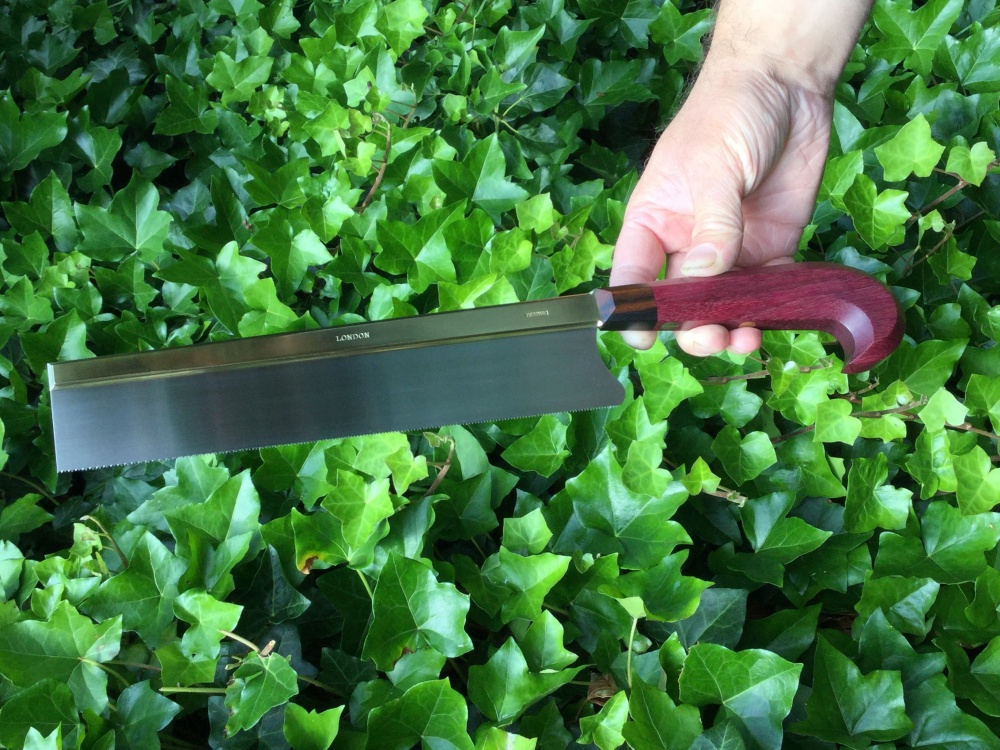
Jacqueline and Shane Skelton have forged a rather unusual business from their home on the outskirts of Scarborough
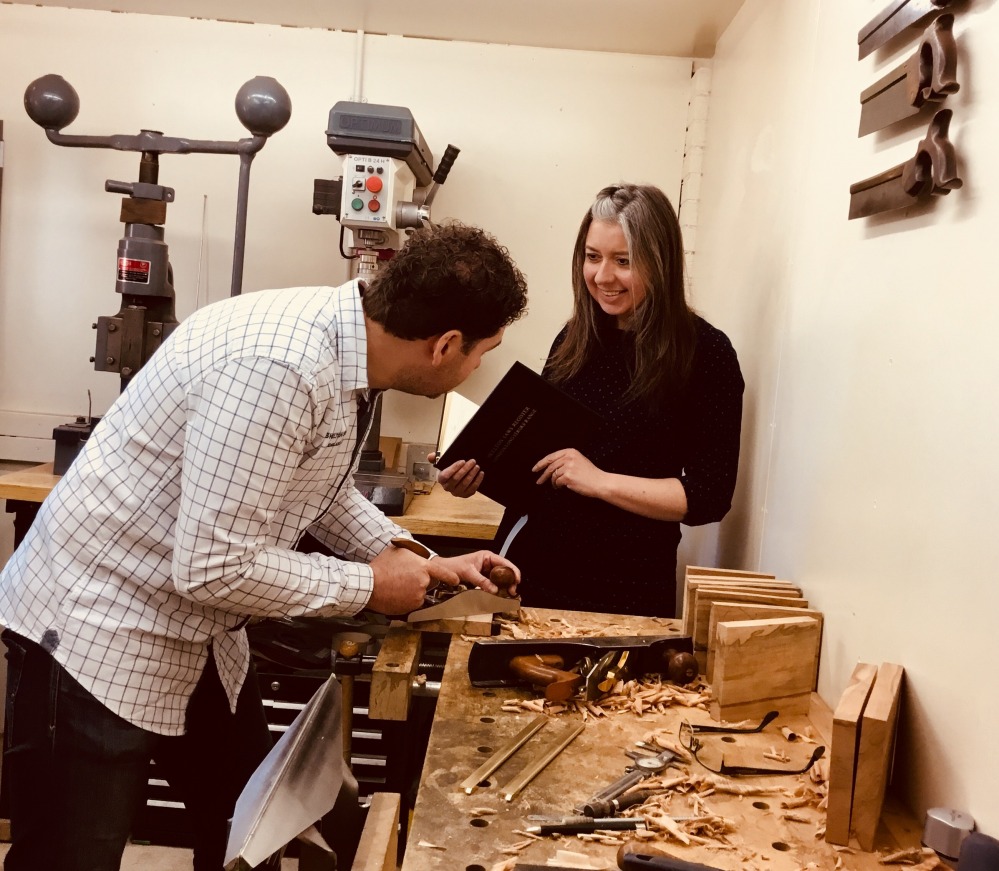
Tell me about your background.
Even before Shane left school, he was working with his hands, spending most weekends working at the local blacksmith’s in Cloughton where even at the tender age of 14 he was forging things like gates for the local church. On leaving school he trained to be a gunsmith with a local business, but after the shop closed down he moved between careers in cabinetmaking and restoration and engineering, and at one point even worked in a small team on the development of a prototype aircraft. I myself trained to be a secondary school teacher, but have also worked in a printing and publishing house before taking time out to raise our two daughters. I think it would be true to say that we both have quite a varied and diverse skillset. Shane is in fact dyslexic, but practically ‘gifted’ as is often the case with people that have this learning difficulty. However, combining all of our skills together works really well: essentially he makes the saws and I run the business.
How did you get started in the world of saws?
Firstly, I should say that running a saw making business wasn’t something we had planned! Shane had always loved and appreciated owning nice tools for his work, but his favourite tool was the saw. He just liked the look of them, the feel of them in the hand when in use and their functionality. However, he’s a perfectionist and could never find one that cut absolutely perfectly straight. For years he kept saying ‘I think I could make something much better’.
So he did?
In 2014 we were in Snainton Woodturning Centre and saw a very nice piece of English Walnut sitting in a corner, and I said ‘why don’t you buy it and have a go at making that saw?’ And so he did! As soon as I saw the finished product, I knew, despite having never picked up a saw in my life, that I could turn this into a business. Having sent the initial dovetail saw to David Charlesworth (one of the county’s most prolific woodworkers) for test, we received amazing praise and reviews and our saw making journey began. All of our saws are traditionally handmade as they were made back in the 18th century. Saw making is currently a critically endangered craft in the UK, and by setting up Skelton Saws we literally brought what was once a thriving craft in Britain back to life.
What is the best thing about what you do?
Without a doubt, for both of us, it is the customer satisfaction. The emails, calls and reviews that we receive from people that are just blown away by Shane’s craftsmanship, often described as ‘functional art’, are really quite humbling. We are both very passionate about what we are doing; Shane in that he is working with his hands to create something that will then go on and make something, more often than not, amazing again. All of our saws have a story, often with a Yorkshire link. For example, the Mallard Saw was initially created to celebrate the work of Sir Nigel Gresley and his Yorkshire-built locomotive. I myself enjoy researching, creating and immersing myself in these stories and then promoting them to people around the globe.
What’s the hardest part?
For Shane, that would definitely be not having enough hours in the day! Anything that is made by hand is time consuming and, when you add the bespoke element to it, you can often run over time. Initially, for me as a woman, I found it hard to establish myself in the essentially male-dominated woodworking world. However, as time has gone on I’ve gained more respect for what we are doing and this has become a little easier. Whilst we both work from home and well together, we can go long periods without any social contact and hence have found it a little isolating at times. Makers do tend to be ‘lone wolves’. We always enjoy going out to events and shows where we showcase our saws and speak to the public, but haven’t been able to do this for the last two years – hopefully we will be able to do this again soon.
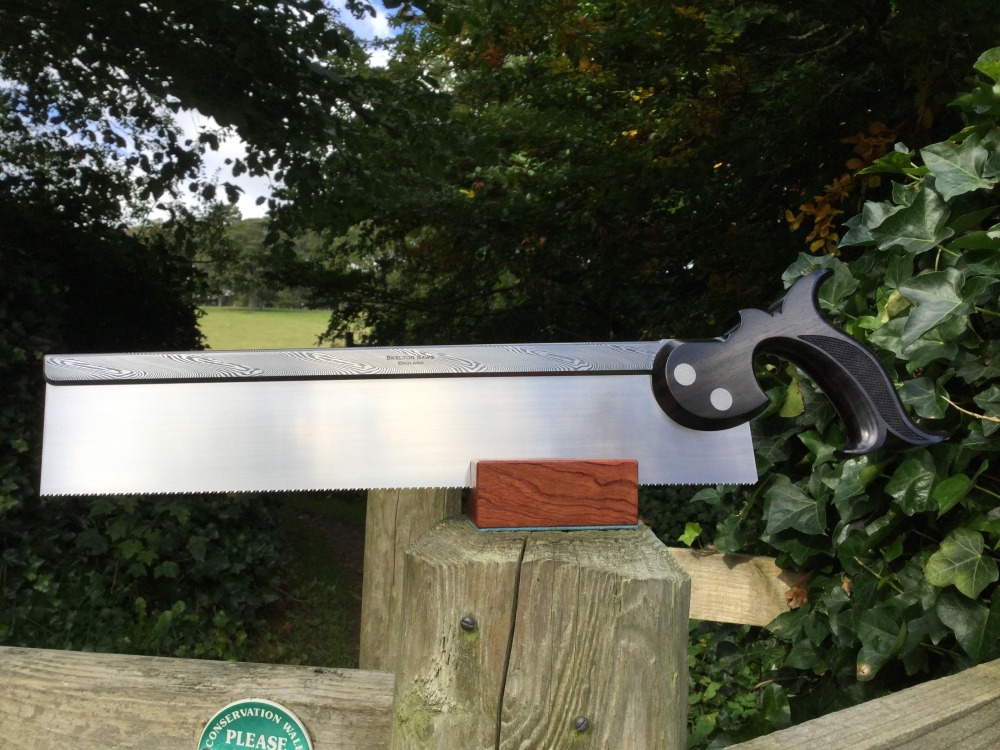
Where do you source materials?
Where possible we try and source our materials locally, all the steel companies we use for example are in Yorkshire. Where possible we use and promote native timbers, and all of the wood that we use comes from sustainable sources. We use only the best quality grades of both metals and woods and have developed a good working relationship with various businesses and independent traders who understand what we are looking for and the quality that we expect. However, one of the most expensive materials that we buy is Damascus Steel. This is hand-forged in Sweden and is from the same source as used by the top London gunmakers. In terms of tooling, this cannot be bought off the shelf, as saw making in the form that we do it no longer really exists, so Shane makes all of his own.
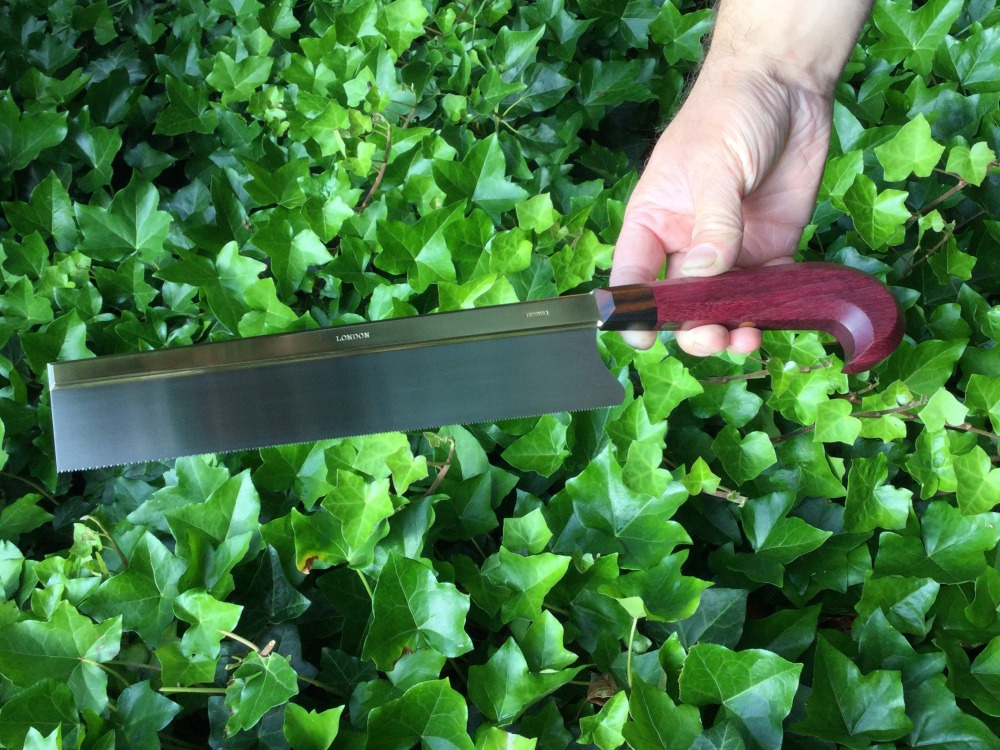
Is there such a thing as a typical day for you?
We have quite a ‘typical day’ in that the structure of our day is always the same. Generally work begins after the school/college run and runs along until pick-up again; we’ll have tea and then Shane will work into the early evening, followed by usually a family walk in Scarborough. In terms of work, what Shane is making is different everyday. We have amassed such a large range of saws now that no two saws tend to be the same on the list each month. I myself spend a lot of time emailing customers, writing about new saws and updating the website and our social media sites, purchasing materials and organising events.
Your saws are all bespoke – why is this?
We don’t believe that ‘one size fits all’. Buying a saw from us is a bit like buying a suit from Saville Row. We measure the customer’s palms and make the handle to fit snugly, so that the saw becomes like an extension of their hand. An off-the-shelf saw can often feel a little cumbersome, and obviously to make good, accurate cuts it’s important to have good control over your tool. We have a growing number of female woodworkers on our books, and they tend to have smaller hands, so they love the fit and control that a custom-made saw provides. Customers can also choose the wood for their handles, the metal for the saw back, the length and how the saw teeth are cut and filed (each one being cut individually by hand using a fly press). This is a very unique service, and not only allows for tastes, but also means that a saw can be made especially to do a certain job. All of our saws are numbered and recorded along with their destinations in our beautiful saw registers, hopefully a historical document of the future.
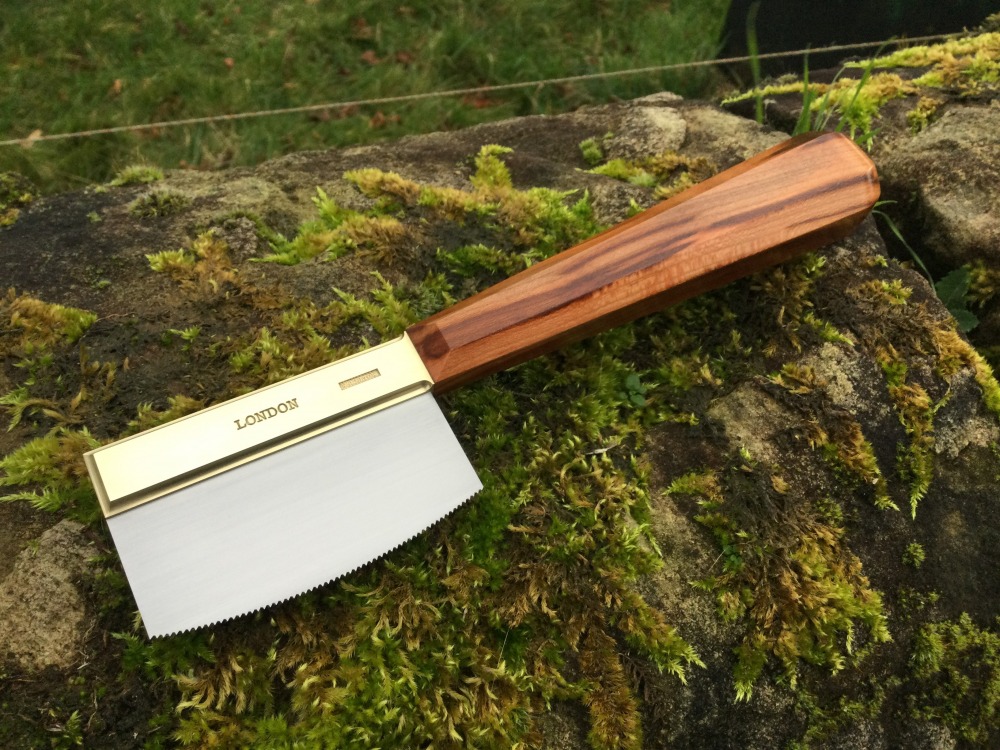
Who are your typical customers?
Our customers range from professional cabinetmakers and luthiers (who want a hand tool that will work with precision) through to hobbyists (who like quality tools) and collectors, some of whom will display them, seeing them as pieces of beautiful art. We send saws all over the world and lots of our customers tend to be lawyers, bankers and doctors for example, so they have stressful jobs but use woodwork as a form of release. The waiting list can often be around a year, and quite often a person will receive their saw and rejoin the list again for something else, which is really encouraging.
Tell us about your most popular type of saw (if you can pick one!).
This is probably the 13 ¾” London Long Stroke Fine Carcass Saw. Its inspiration came from a saw made back in 1760 by a saw maker named William Squire working in Soho, London. It’s a really versatile saw and allows you to do most jobs that the average woodworker would need to do. Currently these saws cost £450 plus postage, for something completely handmade and will last a lifetime. Back in the 18th century a cabinetmaker would spend a week’s wage on a good tool, so that is still pretty relative today.
What’s the most unusual saw you have made?
Recently we have made a saw from the oak from the bell tower of St Paul’s Cathedral. Back in 2018 some of the bells were removed for restoration, for the first time since 1878. The Worshipful Company of Turners in London is funding some of this restoration and, as a gesture of goodwill, were given some of the oak from the headstocks. Last year we were able to acquire a small piece of this oak and make a one-off ‘Chippendale Saw’ with it. We believe the oak could date back to Wren’s time and the building of the Cathedral in the 17th century.
Plans for the future?
Our plan as always is just to keep the art of traditional saw making alive in Britain for as long as we can. It is a work less for profit and more passion for both of us. We always have new ideas and are thinking about new types of saws and ranges going forward. Shane has just finished designing a new dovetail saw which will be unveiled later this year, and again we have both drawn inspiration from some great Yorkshire people. We’ll probably have something special next year to celebrate the Queen’s Jubilee, and hopefully, eventually, we’ll maybe start to look at offering some woodworking courses. Ultimately we are just two people creating something special from a tiny part of Scarborough, and hope that we can keep people smiling with our saws for years to come.